はじめに:
「NACHI」ブランドで有名な総合機械メーカー「不二越」のロボット製造所では、スマート工場化の取り組みが進められています。ロボット製造所長として、名実ともに取り組みを牽引する林 雅樹さんに、取り組みの概要と「DX推進のコツ」をお伺いしました。
●お答えいただいた方
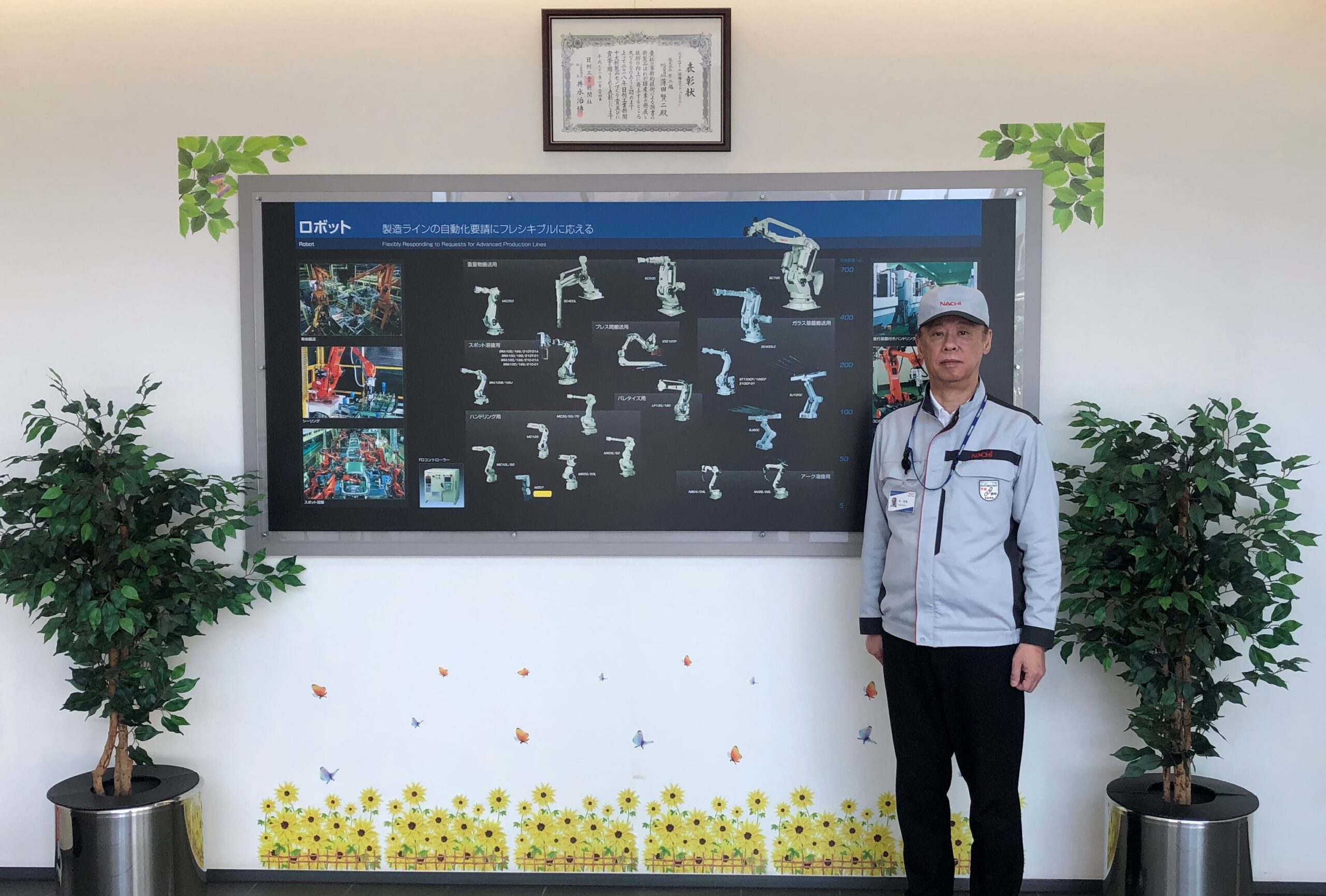
株式会社不二越
ロボット事業部 ロボット製造所長
林 雅樹 さん
「不二越」の事業概要について
事務局:まずは、不二越様の概要について教えてください。
林:不二越は、1928年に富山で創業した総合機械メーカーです。当時、機械工具は輸入に頼っていたのですが、「機械工具分野の自立こそ、わが国の産業を発展させる基礎である」として、機械工具の国産化をめざして創業、最初は「ハクソー」と呼ばれる電動のこぎりの刃の開発から始まりました。その後、不二越の「ハクソー」を優秀国産品として、昭和天皇がご覧になったこともあり、ゆかりのある「NACHI」を商標、マークとして、事業を行っています。会社は、あと四年ほどで創立100周年を迎えます。
事務局:ありがとうございます。まさに、日本の産業の進歩と共に歩んでこられた企業ですね。現在はどのような事業を行っておられるのでしょうか。
林:当社は「モノづくりのプロセスに貢献する」ということで、特殊鋼やサーモテックなどの「マテリアル事業」、工具や工作機械などの「機械工具事業」、ベアリングや油圧機器、カーハイドロリクスなどの「機能部品事業」、そして「ロボット事業」を行っています。「ロボット事業」は、富山と海外に製造拠点がありますが、ロボット製造所長として、私が製造部分を担当しています。
事務局:ありがとうございます。不二越様ではどのようなロボットを作られているのでしょうか。
林:不二越が作っているロボットは、産業用ロボットであり、「垂直多関節ロボット」が主なものとなります。ロボットが持てる重さを「可搬質量」というのですが、可搬質量が1kg~1t程度のロボットを製造しています。ロボット産業が発展した理由の一つは、自動車製造に用いられたことなのですが、自動車製造では、先端にハードガンと呼ばれる機器を接続したスポット溶接や、プレス間搬送等の用途に使われています。また、小型ロボットをリリースし、組立産業などでも導入していただいています。
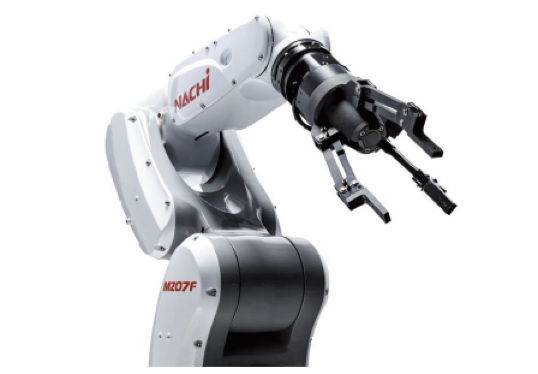
不二越ロボット製造所の”スマート工場化”の取り組み
事務局:では、本題となりますが、不二越ロボット製造所で実施されている”スマート工場化”の取り組みについて、教えてください。
林:まず、2016年に「工場内のフォークリフトの位置情報や稼動状況の見える化」をしたいと思い、MULTISOUPさんという位置測位技術に強い会社さんと、Beaconとスマートフォンを用いた取り組みを実施しました。その後、2018年にBeaconとBluetoothゲートウェイを整備し、「ロボット製造の進捗管理の見える化」を行い、製造リードタイムの26%削減、仕掛在庫数60%削減を実現することができました、また並行して、工場内の安全確保や作業進捗確認を目的として、ネットワークカメラを導入し、併せてWi-Fiの整備を行いました。その結果、富山のロボット工場には、90を超えるWi-Fiの無線アクセスポイントや30台弱のBluetoothのゲートウェイ、200個のBeaconを設置し、通信環境が整いました。
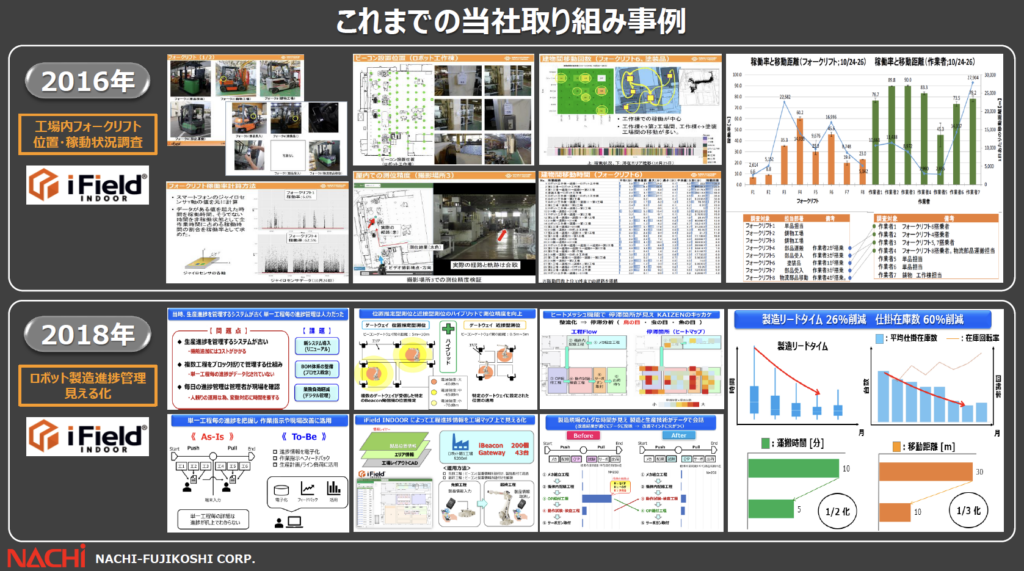
(イメージ:2016年、2018年の取り組み)
事務局:最初から、大規模な通信環境を整備するのではなく、様々なDXに関するチャレンジ、成功事例を作り出しながら、DXの基盤となる通信環境を拡げられたのですね。その後はどのような取り組みをされているのでしょうか。
林:整備した通信環境を活用して様々な取り組みを行っています。例えばWi-Fi環境を使い、「事務所側PCからの工場内PCの遠隔操作」や、「スマートグラスを活用した作業者スキルの遠隔判定」を行っています。また、「スマートフォンを活用した音声によるチェックリストの電子化」に取り組み、作業者がチェックリスト記入に手を止める必要が無いようにしたり、「スマートフォンを活用した作業者の作業動態把握や報告書作成」であったり、「工作機の稼働情報把握」にも取り組んでいます。また、PoCにはなりますが、「スマートウォッチを活用した作業行動分析」にも取り組んでいるところです。
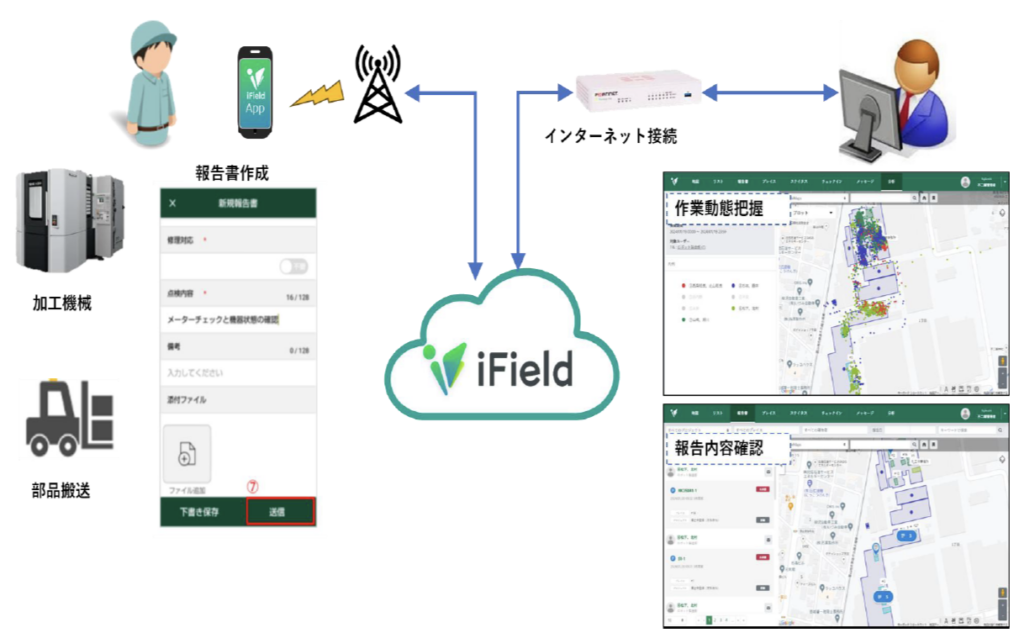
(「スマートフォンを活用した作業者の作業動態把握や報告書作成」のイメージ)
事務局:デジタル活用の取り組みを、同時並行的にかなり多く進めていらっしゃるような印象を受けましたが、取組のコツは何でしょうか。
林:今までやってきたところは「なんちゃってDX」だと思っています。現状の問題を早期に解決したい場合に、「大きなプロジェクト」にすると、例えば予算が取りにくかったり、幹部の決裁が必要になったり等で、取り組むまでの期間が長くなるということは、一般的によくあることだと思います。ですので、我々はまず、自身が決裁できる範囲のプロジェクトにしてしまい、得意な会社を巻き込みながら、「低予算で短期に課題を解決する」ということをやっています。ロボット製造所の中では2023年6月からは、「やっちゃえDXプロジェクト」と名付けて実施しているところです。
事務局:「得意な会社」を巻き込むコツは何なのでしょうか。
林:勘と経験です(笑)。「こういったことをやりたい」と思ったときに、最初はまず私がアクションするのですが、そこで判断しています。2016年の「工場内のフォークリフトの位置情報や稼動状況の見える化」以来、位置測位分野で手伝っていただいているMULTI SOUPの那須社長もその一人です。
事務局:「社内」を巻き込むコツはいかがでしょうか。
林:まず、取り組みについては、ちゃんとした資料を作って、私から作業者に説明します。そして、説明をした後にアンケートを取って、「取り組みへの期待度」を測ります。トップダウンでやるのですが、私はずっと現場にいたので、「現場がもっと楽になる」ということを考えながらやっています。「楽して儲けましょう、そのためにIoTやITを武器として使いましょう」ということをよく言っています。ロボット製造所は若い世代の社員も多く、案の定、上手く使いこなしていると思います。昔から、作業者との対話会をやっています。そういった中で、「こういうことをやってほしい」というディスカッションをしながら、取り組みを進めているところです。
これからのDXについて
事務局:DXを進めるに当たっての林所長の思いをお聞かせください。
林:DXは、行動変容につながらないといけません。「やっちゃえDXプロジェクト」は技能者の意識を変えたい、技能者の変革を起こしたいということで始めました。デジタルデータを活用して技能者が最適解を考え、自ら発信するような、「過去の成功体験を知らないZ世代だからできる新たな技能者」を育てていきたいですね。これが、我々のDXだと思っています。
事務局:DXのコツは何なのでしょうか。
林:色々な企業からDXの相談を受けますが、現状把握、現状分析がちゃんとできていないケースが多いです。科学的に現状を分析していないと、データがあいまいになります。データの裏付けを理解し、そこから問題や課題を抽出しないと真の改善にはつながらないと思います。現状把握をしっかりやっていく必要があると思います。
事務局:先程ご紹介いただいた「取り組み」は、現状把握をするための「インフラ」なのだということがよくわかりました。
林:作業者自身がボトムアップで改善した結果が、翌日にはデータに出てきます。そうすると、みんな面白くなるんですね。その「体験」を色々な工程に横展開している状況です。
次世代通信”スマート工場”で求める通信技術について
事務局:様々な取り組みをやられている中で、次世代通信に求めることはありますか。
林:例えば、ローカル5Gを工場に整備するということにはメリットがあると思います。今後の次世代通信という意味では、現在6Gの開発に向けた動きが進んでいると聞いていますが、まずは「B to C」側で発展し、それを「B to B」に取り込んでいくことになるのではないかと思っています。
事務局:今日は、貴重なお話をありがとうございました。